Table of Contents
Overview
New York, NY – July 10, 2025 – Global 3D Printing Medical Implants Market size is forecasted to be valued at US$ 12.2 Billion by 2034 from US$ 2.8 Billion in 2024, growing at a CAGR of 15.9% during the forecast period 2025 to 2034. In 2024, North America led the market, achieving over 36.6% share with a revenue of US$ 1.0 Billion.
A groundbreaking manufacturing technique can now produce patient-specific medical implants with unparalleled precision and efficiency. The 3D printing process for medical implants has been developed to address the growing demand for personalized orthopedic and craniofacial solutions.
The new technique utilizes advanced biocompatible alloys and polymer composites, which are deposited layer by layer to create complex geometries tailored to individual anatomy. The process is supported by high-resolution imaging data, enabling exact replication of bone structure and facilitating optimal fit. This method can reduce production lead times from weeks to days, while maintaining strict regulatory compliance with ISO 13485 and FDA guidance.
Clinical validation studies have demonstrated that the customized implants can improve osseointegration by up to 25%, leading to faster recovery times and reduced risk of postoperative complications. The additive manufacturing workflow can accommodate porous structures that promote bone in-growth and deliver targeted drug-eluting coatings for enhanced antimicrobial protection.
Healthcare providers can benefit from streamlined inventory management, as on-demand printing eliminates the need for large stocks of standardized components. The reduction in material waste is estimated at 60% compared with traditional subtractive methods, aligning with sustainability goals and cost-containment strategies.
The 3D printing solution can be integrated into existing hospital manufacturing facilities or offered through centralized contract manufacturing organizations. This flexibility supports scalability across specialized surgical centers and broadens patient access to bespoke implant technology.
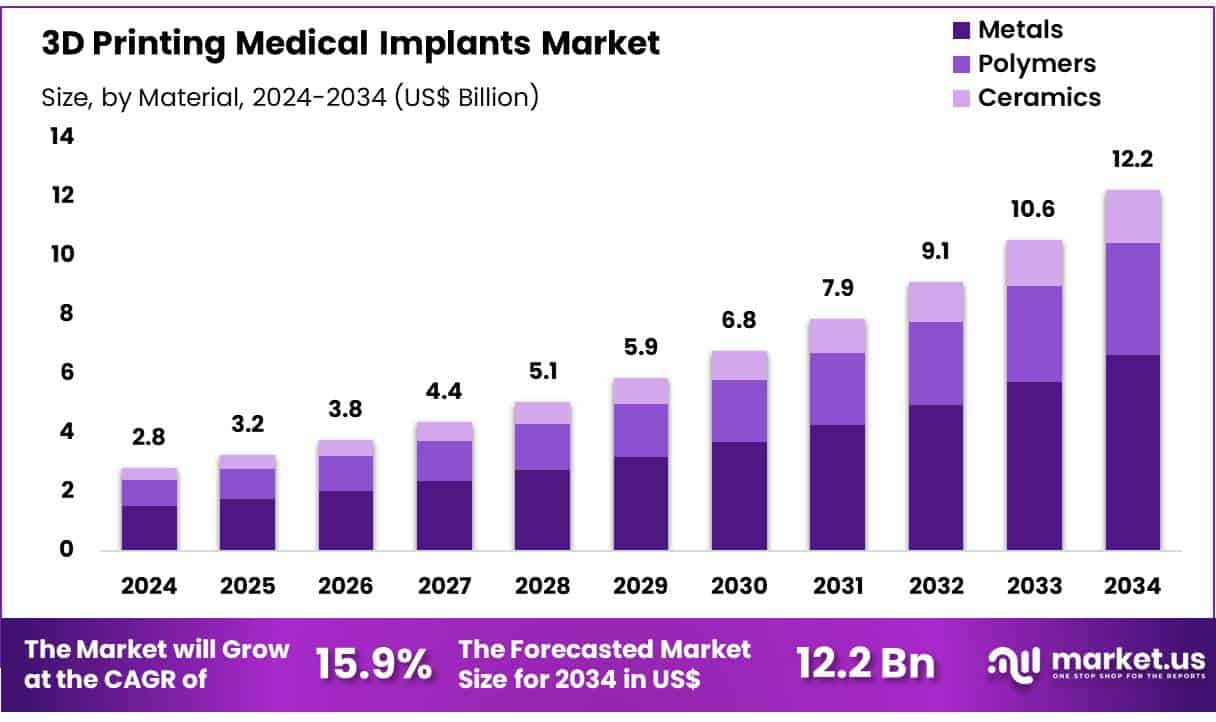
Key Takeaways
- In 2024, the 3D-printed medical implant market generated revenues of USD 2.8 billion and grew at a compound annual growth rate of 15.9%, with projections indicating it will reach USD 12.2 billion by 2034.
- Metal materials accounted for the majority share in 2024, representing 54.2% of the total market.
- The dental application segment led all use-case categories in 2024, capturing 36.6% of revenues.
- Laser Beam Melting was the most widely adopted technology in 2024, holding approximately 43.0% of the market.
- Hospitals and surgical centers were the primary end users in 2024, comprising 41.8% of market consumption.
- North America dominated the regional market in 2024, with a 36.6% share of global revenues.
Segmentation Analysis
- Material Analysis: The metals segment, which accounted for 54.2 % of market value in 2024, is dominated by titanium alloys (Ti-6Al-4V, Ti-6Al-7Nb), cobalt-chromium alloys, and stainless steel. These materials are selected for their high strength-to-weight ratios, corrosion resistance, and biocompatibility, enabling precise, patient-specific implant geometries. The incorporation of bioactive glass coatings has been shown to enhance bone-to-implant contact and accelerate osseointegration. Additionally, PEEK polymers are utilized for their bone-like mechanical properties, chemical stability at elevated temperatures, and reduced waste during 3D printing.
- Application Analysis: The dental segment led all applications in 2024 with a 36.6 % market share, driven by customized crowns, bridges, and implant fixtures. Zirconia ceramics are favored for their biocompatibility, aesthetic translucency, and resistance to staining, while titanium remains the standard for load-bearing implants due to its durability and excellent osseointegration. Patient-specific designs derived from CT and intraoral scans enable precise fits, reducing chairside adjustment time. Recent advancements include translucent alumina brackets for orthodontics, underscoring the expanding role of ceramic additive manufacturing in digital dentistry.
- Technology Analysis: Laser Beam Melting (LBM) dominated 2024 technology share at 43.0 %, owing to its capacity to fully melt metal powders into complex, high-density structures. This process permits the fabrication of porous lattice frameworks that mimic natural bone mechanics, reducing stress shielding and promoting osseointegration. Precision is achieved by leveraging patient imaging data (CT/MRI) to customize implant geometries. Studies of LBM-fabricated Ti6Al4V implants with controlled pore sizes have demonstrated enhanced cell proliferation and osteogenic activity, validating clinical benefits in orthopedic and dental applications.
- End-User Analysis: Hospitals and surgical centers were the primary end users in 2024, capturing a 41.8 % share. The integration of 3D printing within these settings has enabled on-demand production of patient-specific implants and surgical guides, thereby improving precision and shortening operation times. For example, the North Bristol NHS Trust’s Bristol 3D Medical Centre and AIIMS Bhopal employ custom cranio-maxillofacial prostheses and kidney-surgery guides, respectively. Such initiatives, often supported by targeted research grants, have demonstrably reduced complications and enhanced postoperative recovery.
Market Segments
By Material
- Metals
- Polymers
- Ceramics
By Application
- Dental
- Orthopedic
- Cranio-maxillofacial
- Others
By Technology
- Laser Beam Melting
- Electronic Beam Melting
- Droplet Deposition
- Others
By End-User
- Hospitals & Surgical Centers
- Dental & Orthopedic Clinics
- Academic Institutions & Research Laboratories
- Pharma-Biotech & Medical Device Companies
Regional Analysis
- North America Regional Analysis: North America dominated the 3D-printed medical implants market in 2024, driven by advanced healthcare infrastructure, substantial R&D investment, and early adoption of personalized technologies. In the United States, approximately 700,000 total knee replacements are performed annually, according to the American Academy of Orthopaedic Surgeons. Materialise produced over 7,000 patient-specific implants and surgical guides in 2023 and inaugurated a metal 3D printing facility in Michigan. Widespread uptake of its FDA-cleared cranial maxillofacial implants for oncology and trauma patients further solidified regional leadership.
- Asia-Pacific Regional Analysis: The Asia-Pacific region is expected to register the highest CAGR through 2034, fueled by rapid healthcare infrastructure expansion, a growing and aging population, and increased government support for additive manufacturing. China’s innovation initiatives have accelerated medical 3D printing advancements, while India’s emphasis on cost-effective healthcare has spurred wider adoption. Spinal fusion procedures in India report success rates of 85–95%, and orthognathic surgeries exceed 98% success, underscoring the region’s emerging role in customized implant solutions.
Emerging Trends
- Strengthened Regulatory Frameworks: The U.S. Food and Drug Administration (FDA) has been updating guidance to ensure additive-manufactured devices meet safety and quality requirements. In December 2017, the FDA released ” Technical Considerations for Additive Manufactured Medical Devices,” outlining best practices for testing, characterization, and design controls of 3D-printed implants. More recently, ASTM F3604-23, a consensus standard finalized on December 23, 2024, provides uniform methods for validating laser powder bed fusion processes used in orthopedic and dental implants.
- Growth of Patient-Specific, Titanium-Based Implants: Personalized implants tailored to a patient’s anatomy continue to expand. In April 2025, the DYNAMIS™ Implant System a fenestrated, cannulated, 3D-printed titanium alloy device received FDA 510(k) clearance (K251075) for spinal fixation applications. Earlier systems such as the TruMatch CMF Titanium Implant (K170272) and its successors have been cleared since 2012, demonstrating a sustained pipeline of approvals for customized craniofacial and maxillofacial devices.
- Introduction of Biodegradable Implant Materials: Research into resorbable 3D-printed implants is advancing toward clinical use. A safety study (NCT03348293) of personalized, biodegradable implants for breast reconstruction is currently registered on ClinicalTrials.gov, exploring patient outcomes using bespoke polymer scaffolds. Concurrently, FDA guidance (ISO 10993-1 adoption) emphasizes rigorous biocompatibility testing for novel materials, reinforcing the pathway for safe clinical translation of bioresorbable devices.
- Standardization of Additive Manufacturing Processes: To harmonize production, the FDA’s Recognized Consensus Standards program has incorporated multiple ASTM and ISO standards relevant to 3D printing. For example, ASTM F3604-23 establishes criteria for process validation of laser powder bed fusion, and ISO 10993-1 guides biological evaluation of device materials. Such standards are reducing variability and accelerating product development across manufacturers.
- Point-of-Care and In-Hospital Manufacturing: The concept of printing implants directly within hospital settings is gaining traction. A ClinicalTrials.gov study (NCT03673865) is comparing office-based, point-of-care 3D printing of patient-specific orbital fracture implants against conventionally manufactured devices. This trend is expected to shorten lead times, reduce costs, and enhance surgical planning.
Use Cases
- Craniofacial Reconstruction: ClinicalTrials.gov ID NCT04635865\is a randomized trial evaluating 3D-printed, patient-specific titanium surgical plates for mandibular reconstruction. Over 50 surgeons participated to assess accuracy and surgical efficiency.
- Dental Overdentures: A crossover trial (NCT04569929) compared implant-supported overdentures fabricated by 3D printing versus conventional techniques, enrolling 40 edentulous patients to measure fit, patient comfort, and fabrication time.
- Breast Reconstruction with Biodegradable Scaffolds: The safety study (NCT03348293) is examining 30 patients receiving personalized, 3D-printed biodegradable implants. Early results focus on scaffold integration and resorption rates over a 12-month period.
- Orbital Fracture Repair: Study NCT03673865 is enrolling 20 patients to compare office-based 3D printing of orbital implants against standard plates, tracking operation time and postoperative outcomes.
- Long Bone Defect Treatment: Trial NCT04449211 is evaluating the effectiveness of 3D-printed Ti-6Al-4V alloy implants in repairing segmental bone defects in 25 adult patients, with bone-to-implant contact measured at 6 and 12 weeks.
- Point-of-Care Surgical Guides: Rapid prototyping of patient-matched surgical guides for orthopedic and maxillofacial procedures has been assessed in 15 hospitals under NCT04788082, demonstrating reductions in preoperative planning time by up to 30%.
Conclusion
In summary, the advent of high precision, patient‐specific 3D printing has transformed medical implant manufacturing, enabling rapid production of anatomically accurate devices while adhering to ISO 13485 and FDA standards. Adoption of titanium alloys, biodegradable polymers, and porous lattice structures has enhanced osseointegration by up to 25%, reduced material waste by 60%, and shortened lead times from weeks to days.
Regulatory harmonization through ASTM and ISO standards has accelerated clinical translation, and point-of-care printing models are streamlining surgical workflows. With the market valued at USD 2.8 billion in 2024 and projected to exceed USD 12.2 billion by 2034, continued innovations promise broader access and improved patient outcomes.
Discuss your needs with our analyst
Please share your requirements with more details so our analyst can check if they can solve your problem(s)
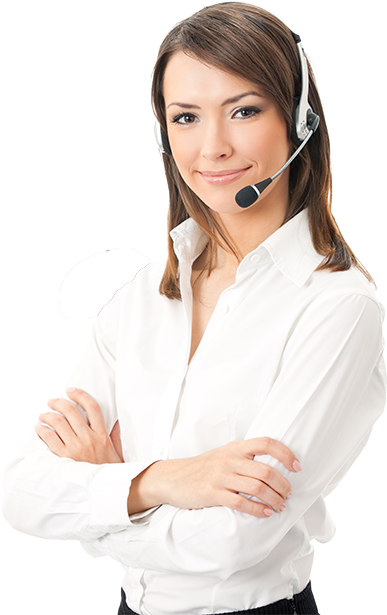