Table of Contents
Introduction
Global Process Analytical Technology Market size is expected to be worth around USD 10.6 Billion by 2032 from USD 3.4 Billion in 2023, growing at a CAGR of 13.8% during the forecast period from 2024 to 2032.
The Process Analytical Technology (PAT) market is a rapidly evolving field, driven by the need for real-time monitoring and control in pharmaceutical manufacturing. The U.S. Food and Drug Administration (FDA) has established a framework that encourages the use of PAT to enhance pharmaceutical development, manufacturing, and quality assurance. This framework supports innovation by addressing technical and regulatory challenges, promoting the adoption of advanced analytical technologies in the pharmaceutical industry.
Key growth factors in the PAT market include the increasing demand for consistent product quality and the implementation of Quality by Design (QbD) principles. PAT enables manufacturers to monitor critical process parameters in real-time, ensuring that pharmaceutical products meet regulatory standards. This technology is particularly important in continuous biomanufacturing, where real-time data allows for immediate adjustments, improving efficiency and reducing waste.
However, the market faces several challenges. High initial investment costs and the complexity of integrating PAT with existing manufacturing processes can hinder adoption. Additionally, a shortage of skilled professionals to operate these advanced systems remains a significant barrier. Despite these challenges, recent advances in technology, such as the integration of PAT with digital and automation technologies, are helping to overcome these obstacles.
Key Takeaways
- Market Size: Global process analytical technology market size is expected to be worth around USD 10.6 Billion by 2032 from USD 3.4 Billion in 2023
- Market Growth: The market growing at a CAGR of 13.8% during the forecast period from 2023 to 2032.
- By Technology Analysis: The spectroscopy segment is the most llucrative in the global process analytical technology market. The total revenue share of spectroscopy process analytical technology is 43.1% in 2022.
- By Product & Service Analysis: The analyzer’s product and service segment is estimated to be the most lucrative segment in the global process analytical technology market, with a market share of 32% in 2022.
- By Application Analysis: The large molecule segment is estimated to be the most dominant segment in the global process analytical technology market.
- By Measurement Analysis: The in-line segment is estimated to be the most lucrative segment in the global process analytical technology market.
- By End-User Analysis: The pharmaceutical manufacturers segment is estimated to be the most dominated segment in the global process analytical technology market.
- Regional Analysis: North america is estimated to be the most lucrative market in the global process analytical technology market, with the largest market share of 33.8%, and is expected to register a CAGR of 8.1% during the forecast period.
- Regulatory Support: The FDA has established a framework that encourages the use of PAT, promoting innovation in pharmaceutical manufacturing and quality assurance.
- Quality Control Focus: PAT is essential for maintaining consistent product quality and compliance with regulatory standards, especially through real-time monitoring of critical process parameters.
Process Analytical Technology Statistics
- PAT implementation can reduce drug development time by 15-30%, accelerating the time to market for new pharmaceuticals.
- The use of PAT has been shown to reduce production costs by up to 50% through real-time monitoring and control of manufacturing processes.
- Over 75% of pharmaceutical companies have integrated PAT into their manufacturing processes, reflecting its growing importance in the industry.
- PAT is expected to be utilized in 90% of new pharmaceutical manufacturing facilities by 2025, driven by the demand for quality assurance and efficiency.
- The adoption of PAT has led to a 20-30% improvement in the quality consistency of pharmaceutical products.
- Real-time release testing (RTRT) enabled by PAT can reduce product release time from weeks to just hours.
- 60% of companies that use PAT report improved compliance with regulatory requirements due to better process control and data transparency.
- PAT tools can monitor 100% of critical process parameters in real-time, ensuring that every batch meets quality standards.
- The FDA encourages the use of PAT to achieve a 30-40% reduction in product recalls related to manufacturing defects.
- 80% of the data generated by PAT systems is used to optimize manufacturing processes, leading to continuous improvement.
- PAT systems can reduce the need for off-line testing by up to 90%, streamlining the quality assurance process.
- The pharmaceutical industry has seen a 25% reduction in process variability after implementing PAT, leading to more consistent product quality.
- PAT adoption is linked to a 20-25% increase in manufacturing efficiency, resulting in significant cost savings.
- 50-70% of all new drug applications now include PAT strategies as part of their quality assurance framework.
- PAT has helped reduce the environmental impact of pharmaceutical manufacturing by 15-20% through optimized resource use and waste reduction.
Process Analytical Technology Application Analysis
- Small Molecules: In small molecule pharmaceuticals, PAT is crucial for monitoring and controlling chemical reactions and crystallization processes. It ensures precise dosage and consistent quality in drug production, contributing to 20-30% fewer deviations during manufacturing. PAT tools like Near-Infrared Spectroscopy (NIR) are commonly used for real-time analysis of small molecules.
- Large Molecules: For large molecules, including biologics, PAT is used to monitor protein folding, aggregation, and glycosylation in real-time. This application is vital for maintaining the structural integrity of complex biologics, reducing batch failures by up to 25%. Techniques like Raman spectroscopy and liquid chromatography are widely employed in this segment.
- Manufacturing Applications: PAT’s application in manufacturing extends to in-line monitoring, ensuring process parameters remain within specifications. This approach reduces production cycle times by 15-20% and minimizes waste, improving overall manufacturing efficiency. PAT tools help achieve consistent product quality by enabling real-time adjustments during production.
Emerging Trends
- Real-Time Monitoring: PAT enables real-time monitoring of pharmaceutical manufacturing processes, allowing for immediate adjustments and improvements in product quality.
- Noninvasive Technologies: Advances in noninvasive PAT, such as water proton Nuclear Magnetic Resonance (wNMR), are emerging. These technologies allow drug products to be analyzed within their containers, ensuring product integrity and improving efficiency.
- Quality by Design (QbD): The integration of PAT with QbD principles continues to grow, enabling more precise control over manufacturing processes and ensuring consistent product quality.
- Continuous Manufacturing: The shift from batch to continuous manufacturing is gaining momentum, with PAT playing a crucial role in monitoring and controlling continuous processes, reducing variability, and improving efficiency.
- Automation Integration: PAT systems are increasingly being integrated with automation technologies, reducing manual intervention, enhancing process control, and improving manufacturing efficiency.
- Regulatory Support: The FDA’s framework for PAT encourages the adoption of advanced analytical technologies, supporting innovation in pharmaceutical manufacturing and ensuring compliance with regulatory standards.
- Data-Driven Decision Making: The use of PAT in conjunction with advanced data analytics tools is becoming more prevalent, helping manufacturers make informed decisions based on real-time data and improving overall process understanding.
Use Cases
- Continuous Manufacturing: PAT tools, such as spectroscopy and microscopy, play a crucial role in continuous manufacturing processes by ensuring real-time monitoring and control, which helps maintain consistent product quality. For example, in the continuous crystallization of drug substances, PAT helps manage particle size and purity.
- Quality by Design (QbD): PAT supports the implementation of QbD frameworks by enabling real-time data collection and analysis. This helps manufacturers design processes that consistently produce high-quality products, reducing variability and enhancing efficiency.
- Crystallization Monitoring: In continuous crystallization processes, PAT tools like Raman spectroscopy and focused beam reflectance microscopy allow precise monitoring of critical parameters. This ensures that the final product meets the desired specifications.
- Real-Time Control: PAT enables feedback and feedforward control mechanisms within manufacturing processes. This capability allows for immediate adjustments to process parameters, reducing waste and improving efficiency.
- Regulatory Compliance: The adoption of PAT in pharmaceutical manufacturing is encouraged to ensure compliance with regulatory standards. PAT helps meet Good Manufacturing Practices (GMP) by enabling continuous monitoring and control of manufacturing processes.
- Automation Integration: PAT tools are often integrated with automated systems to enhance process control in pharmaceutical manufacturing. This integration supports more reliable and consistent production outcomes.
- Terahertz Spectroscopy: PAT’s application in terahertz spectroscopy allows for non-invasive, real-time analysis of pharmaceutical products, enhancing quality assurance and ensuring product safety during manufacturing.
- Data-Driven Decision Making: By providing real-time data, PAT supports informed decision-making in manufacturing. This allows for proactive adjustments to maintain product quality and optimize efficiency throughout the production process.
Conclusion
The Process Analytical Technology (PAT) market is positioned for substantial growth due to its vital role in enhancing product quality, regulatory compliance, and operational efficiency in pharmaceutical manufacturing. PAT supports real-time monitoring and control, which are critical for maintaining consistent production standards. The market is benefiting from advancements in digital transformation, which allow for more integrated monitoring and optimization systems. As pharmaceutical and biotechnology companies continue to adopt Quality by Design (QbD) principles, PAT will remain essential in meeting stringent quality and regulatory requirements, driving further innovation and market expansion.
Discuss your needs with our analyst
Please share your requirements with more details so our analyst can check if they can solve your problem(s)
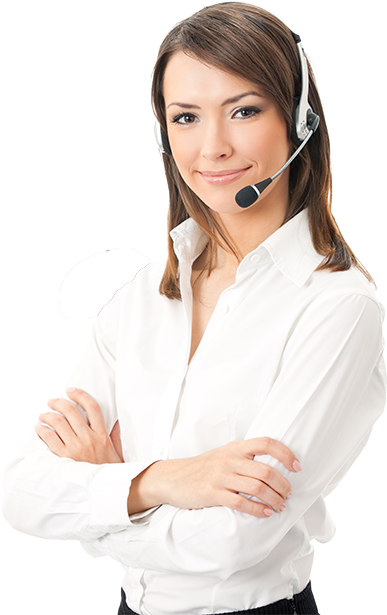