Table of Contents
Introduction
New York, NY – January 17, 2025 – The Global Plastic Injection Molding for Medical Device Market size is expected to be worth around US$ 37.8 Billion by 2033 from US$ 24.6 Billion in 2023, growing at a CAGR of 4.4% during the forecast period from 2024 to 2033. With a market share over 39.5%, North America held a strong lead in 2023, reaching US$ 9.7 Billion in revenue.
The global Plastic Injection Molding for Medical Device Market is experiencing significant growth, driven by the increasing demand for precision, efficiency, and cost-effective production of medical devices. Plastic injection molding is a key manufacturing process used to create complex medical components, such as syringes, IV components, diagnostic devices, and surgical instruments. The technology enables the high-volume production of intricate parts with tight tolerances, which is crucial for the medical industry’s need for reliability and safety.
Factors such as the rising adoption of disposable medical devices, advancements in material science, and the demand for lightweight and durable medical products are contributing to the market’s expansion. The market is also benefiting from regulatory pressure on manufacturers to ensure consistent product quality, which plastic injection molding can provide.
The growing focus on personalized medicine, coupled with the increasing use of medical devices in home healthcare, is expected to further propel market growth. North America is currently the largest market, driven by stringent healthcare regulations and the presence of leading manufacturers.
However, the Asia Pacific region is emerging as a key growth area, thanks to cost advantages and rapid technological adoption. With ongoing innovation in materials and design, the plastic injection molding for medical devices market is poised for continued growth, offering opportunities for manufacturers and suppliers worldwide.
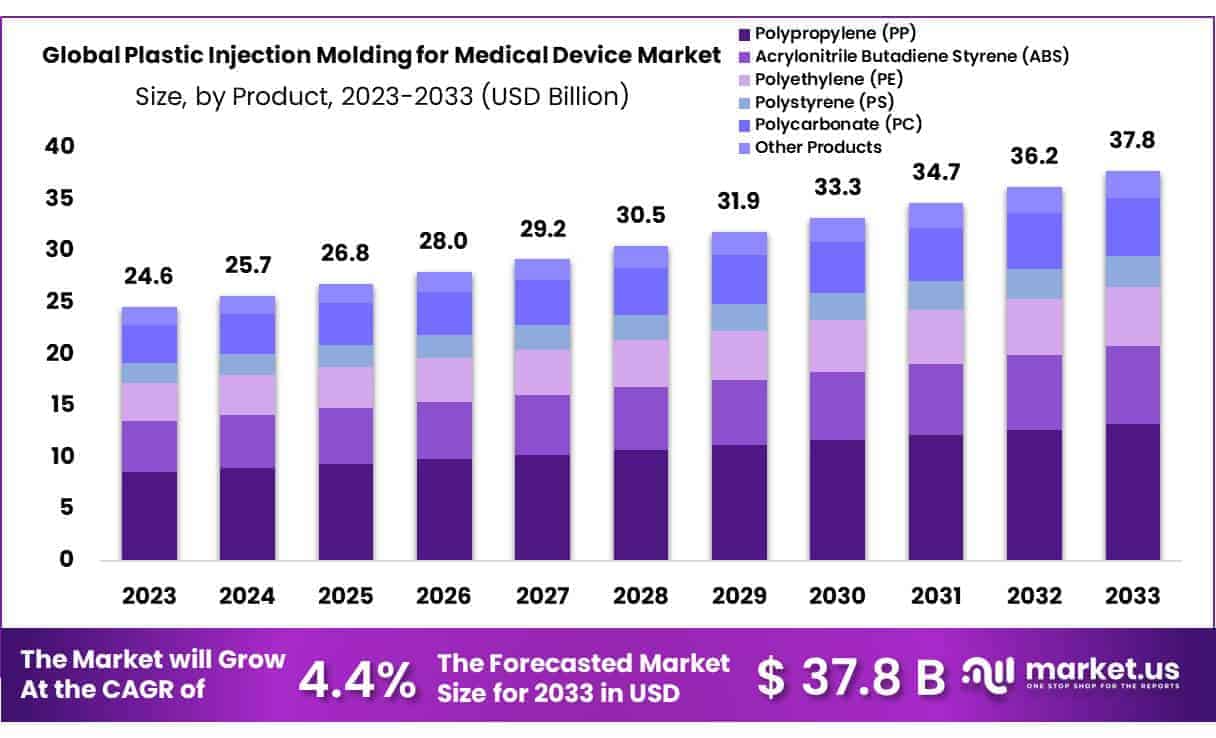
Key Takeaways
- Market Size: The Plastic Injection Molding for Medical Device market is projected to reach USD 37.8 billion by 2033, growing from USD 24.6 billion in 2023.
- Market Growth: The market is expected to grow at a compound annual growth rate (CAGR) of 4.4% from 2024 to 2033.
- Product Analysis: Polypropylene (PP) is the leading material, holding a 35.1% market share, due to its versatility and cost-effectiveness.
- Application Analysis: Medical components represent the largest application segment, accounting for 25.2% of the total market share.
- Regional Analysis: North America is the dominant region, capturing 39.5% of the market share in 2023.
How Artificial Intelligence (AI) is Changing the Plastic Injection Molding for Medical Device Market?
- Improved Quality Control: AI-powered systems are used to detect defects during the production process, enhancing the consistency and reliability of molded plastic products. Automated AI systems can perform real-time inspection of each product, ensuring that the medical devices meet stringent regulatory standards.
- Predictive Maintenance: AI helps predict when injection molding equipment is likely to fail or need maintenance, minimizing downtime and reducing operational costs. This leads to more efficient production schedules, higher productivity, and lower maintenance expenses.
- Optimized Design: AI algorithms are being employed to optimize mold design by simulating and testing different mold geometries, which helps in creating more complex and precise designs for medical devices. This reduces the time and cost required for physical prototypes and trial runs.
- Increased Automation: AI facilitates automation in the injection molding process, allowing machines to adjust automatically based on variables such as material characteristics and environmental conditions. This leads to increased speed and efficiency while maintaining high standards in quality control.
- Enhanced Supply Chain Management: AI tools are being used to optimize supply chains for plastic injection molding in the medical sector. By analyzing data patterns, AI can predict demand and assist with material procurement, reducing delays and ensuring a consistent supply of materials for production.
- Energy Efficiency: AI systems help in managing energy consumption by predicting the most energy-efficient settings for injection molding machines, contributing to sustainability efforts and reducing energy costs.
- Customization of Medical Devices: AI helps in the mass production of customized plastic components, especially for personalized medical devices. This customization can cater to patient-specific requirements, improving outcomes for medical treatments.
- Regulatory Compliance: AI tools help manufacturers stay compliant with medical device regulations by monitoring every step of the production process and ensuring that quality control measures are strictly followed. This includes tracking batch production and providing data for audit trails.
- Data-Driven Decision Making: The use of AI in injection molding helps gather real-time data, which can be analyzed to make informed decisions, from process improvements to material selection and defect prediction.
Product Analysis
- Polypropylene (PP): PP is a versatile thermoplastic polymer known for its chemical resistance, low density, and high melting point. In medical devices, PP is commonly used for components such as syringes, specimen containers, and diagnostic test kits. Its biocompatibility and resistance to sterilization methods like autoclaving make it a preferred choice for single-use medical products.
- Acrylonitrile Butadiene Styrene (ABS): ABS is a thermoplastic polymer characterized by its strength, rigidity, and impact resistance. It is utilized in medical devices such as inhalers, nebulizers, and certain surgical instruments. However, compatibility with specific drugs is crucial; for instance, the FDA has warned against using Treanda Injection with devices containing polycarbonate or ABS due to potential dissolution upon contact with certain chemicals.
- Polyethylene (PE): PE is a widely used thermoplastic polymer known for its chemical resistance and low friction properties. In the medical field, PE is employed in applications such as surgical drapes, catheters, and prosthetic components. Its biocompatibility and ease of sterilization make it suitable for various medical applications.
- Polystyrene (PS): PS is a thermoplastic polymer known for its clarity and ease of processing. It is commonly used in medical devices such as petri dishes, test tubes, and diagnostic trays. PS is valued for its transparency, allowing for easy visualization of contents, and is suitable for single-use applications.
- Polycarbonate (PC): PC is a high-performance thermoplastic polymer known for its strength, transparency, and impact resistance. It is used in medical devices such as blood oxygenators, IV connectors, and surgical instruments. PC’s optical clarity and durability make it suitable for applications requiring high strength and transparency.
- Other Products: In addition to the aforementioned materials, other polymers such as Polyetheretherketone (PEEK), Polyetherimide (PEI), and Polyvinyl Chloride (PVC) are also utilized in medical device manufacturing. Each material is selected based on specific requirements such as biocompatibility, mechanical strength, and sterilization compatibility.
Emerging Trends in Plastic Injection Molding for Medical Devices
- Advanced Materials: The use of high-performance polymers like Polyetheretherketone (PEEK) and Polyetherimide (PEI) is increasing. These materials provide superior strength and biocompatibility, essential for medical applications.
- Micro-Injection Molding: This technique produces extremely small and precise components, crucial for devices such as microfluidic systems and miniature sensors. It enables the creation of complex geometries with high accuracy.
- Overmolding and Insert Molding: These processes involve molding multiple materials simultaneously or adding components like metal inserts into plastic parts. They enhance functionality and reduce assembly steps, leading to more efficient production.
- Automation and Industry 4.0 Integration: The incorporation of automation and smart manufacturing technologies, such as the Internet of Things (IoT) and artificial intelligence (AI), is streamlining production processes. This integration allows for real-time monitoring, predictive maintenance, and improved quality control.
- Sustainability Practices: There is a growing emphasis on using eco-friendly materials and reducing energy consumption. Manufacturers are adopting sustainable practices to minimize environmental impact and comply with regulatory standards.
Use Cases of Plastic Injection Molding in Medical Devices
- Syringes and Needles: Manufacturers produce over 50 million syringes per month using injection molding, ensuring high-quality, single-use medical devices.
- Implantable Components: The process is used to create components for joint replacements and surgical implants, offering durability and biocompatibility.
- Diagnostic Equipment: Injection molding produces test tubes, petri dishes, and other labware, facilitating efficient and sterile diagnostic procedures.
- Drug Delivery Systems: Components for inhalers and nebulizers are manufactured using injection molding, ensuring precise dosing and reliability.
- Orthopedic Devices: The technique is utilized to produce braces and supports, providing strength and comfort for patients.
Conclusion
The global Plastic Injection Molding for Medical Device market is experiencing substantial growth, driven by the increasing demand for high-precision, cost-effective, and reliable manufacturing of medical devices. Advancements in material science, rising demand for disposable medical devices, and innovations in AI are fueling this growth. Polypropylene remains the dominant material, and North America continues to lead the market, though Asia Pacific is emerging as a key growth region.
The integration of AI in quality control, maintenance, design optimization, and supply chain management is transforming production efficiency and regulatory compliance. With emerging trends like micro-injection molding, automation, and sustainability practices, the market is poised for sustained expansion, presenting opportunities for manufacturers and suppliers in the coming years.
Discuss your needs with our analyst
Please share your requirements with more details so our analyst can check if they can solve your problem(s)
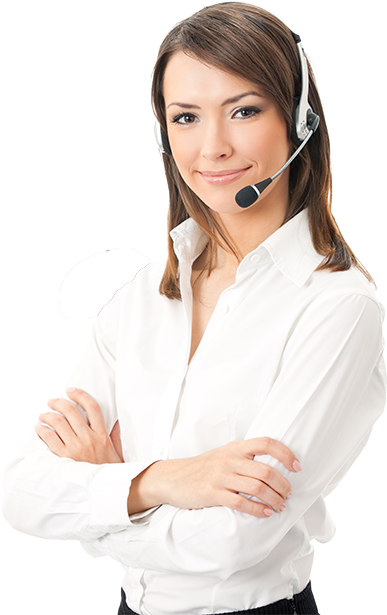